CBN and PCD cutters
Casting in China has existed for thousands of years of history. From the Bronze Age to the industrial revolution. The machinery industry is inseparable from the casting, casting technology represents the level of national mechanical industry. Machinery industry to the plane, high-speed train parts, ship machinery, engineering machinery, power equipment, etc.. The equipment manufacturing industry, small to the basin of boiler bowl gourd ladle in the casting process. Such as when we see the countryside cast aluminum pots, aluminum pots, etc..
Casting workpiece can divide into two categories from the material: one is black metal castings such as gray cast iron, nodular cast iron, alloy cast iron, and cast steel. One is non - ferrous metal casting such as cast copper alloy, cast aluminum alloy. With the development of the mechanical industry, the performance of various casting alloys has been greatly improved. And casting parts machining is more and more used high-speed cutting and dry cutting. High-speed cutting and dry cutting tool development is the most rapid cubic boron nitride tool (CBN tool) and diamond tool (PCD tool). As the "teeth" of the industry, CBN and PCD tools provide the basis for difficult to process materials and batch high-speed cutting of castings.
Application of CBN and PCD tools
The domestic CBN and PCD cutters market has also expanded with the development of tool technology. At present, China's First Automobile Group has more than 100 CBN and PCD cutters. Many wood-based panel companies also use CBN and PCD cutters for wood products processing. The application of CBN and PCD cutters has furthered the research on its design and manufacturing technology. At present, the processing range of CBN and PCD cutters has expanded from traditional metal cutting processing to processing of stone processing, wood processing, metal matrix composites, glass, engineering ceramics, and other materials. From the analysis of CBN and PCD cutters applications in recent years, CBN and PCD cutters are mainly used in the following two aspects:
1. Processing of difficult-to-machine non-ferrous materials: When machining difficult-to-machine non-ferrous materials with ordinary tools. Defects such as easy tool wear and low processing efficiency are often produced, while CBN and PCD cutters can exhibit good processing performance. If use CBN and PCD cutters, the new engine piston material, hyper eutectic silicon aluminum alloy, can effectively process (the research on the processing mechanism of this material has made a breakthrough).
2. Processing of difficult-to-machine non-metallic materials: CBN and PCD cutters are ideal for processing difficult-to-machine non-metallic materials such as stone, hard carbon, carbon fiber reinforced plastic (CFRP), and artificial boards. At present, the application of laminate flooring and other wood-based panels (such as MDF) is becoming more and more widespread. The processing of these materials with CBN and PCD cutters can effectively avoid defects such as the easy wear of the cutter.
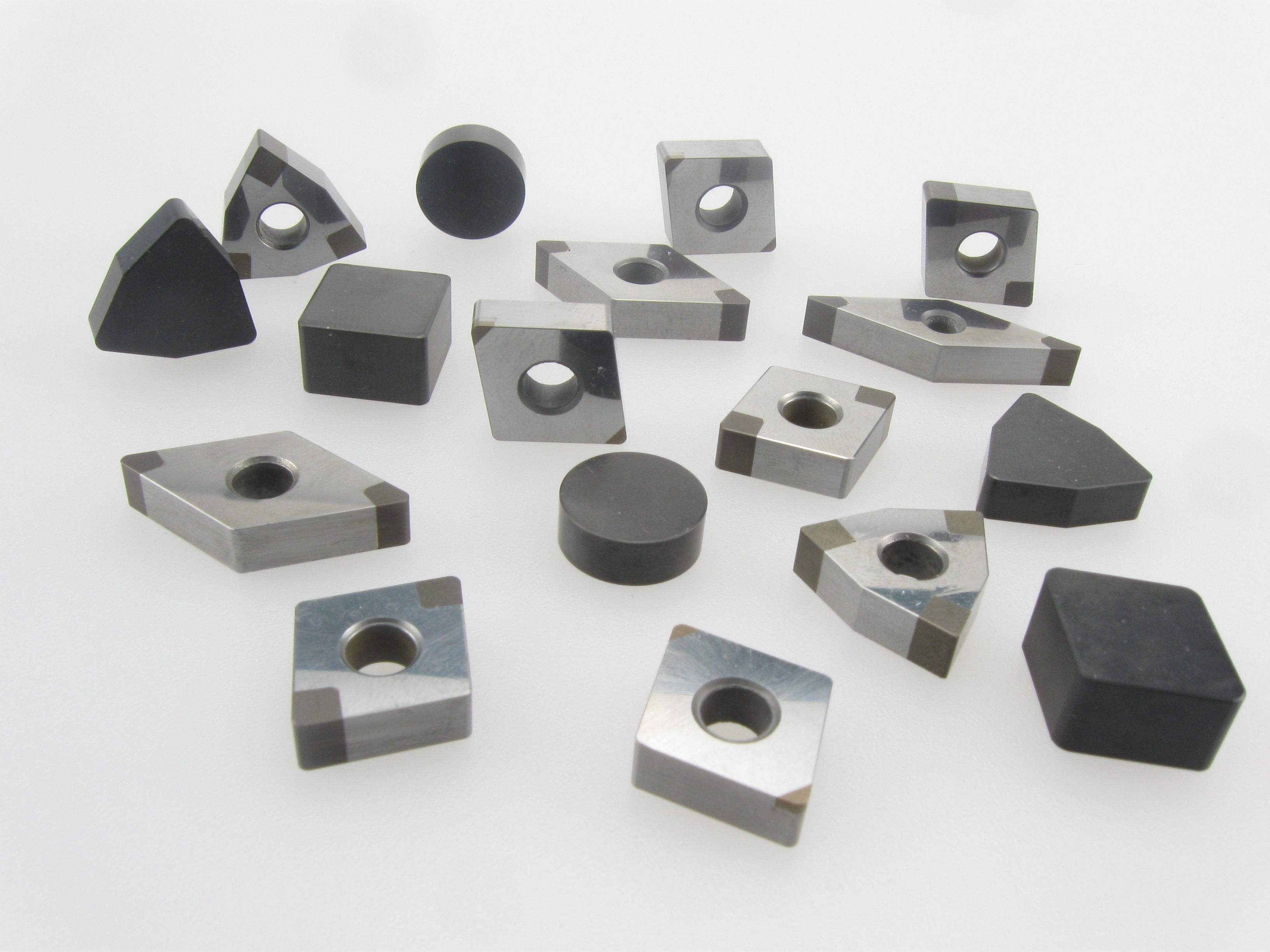